世界に誇る技術を証明した
ギヤポンプ内製化プロジェクト。
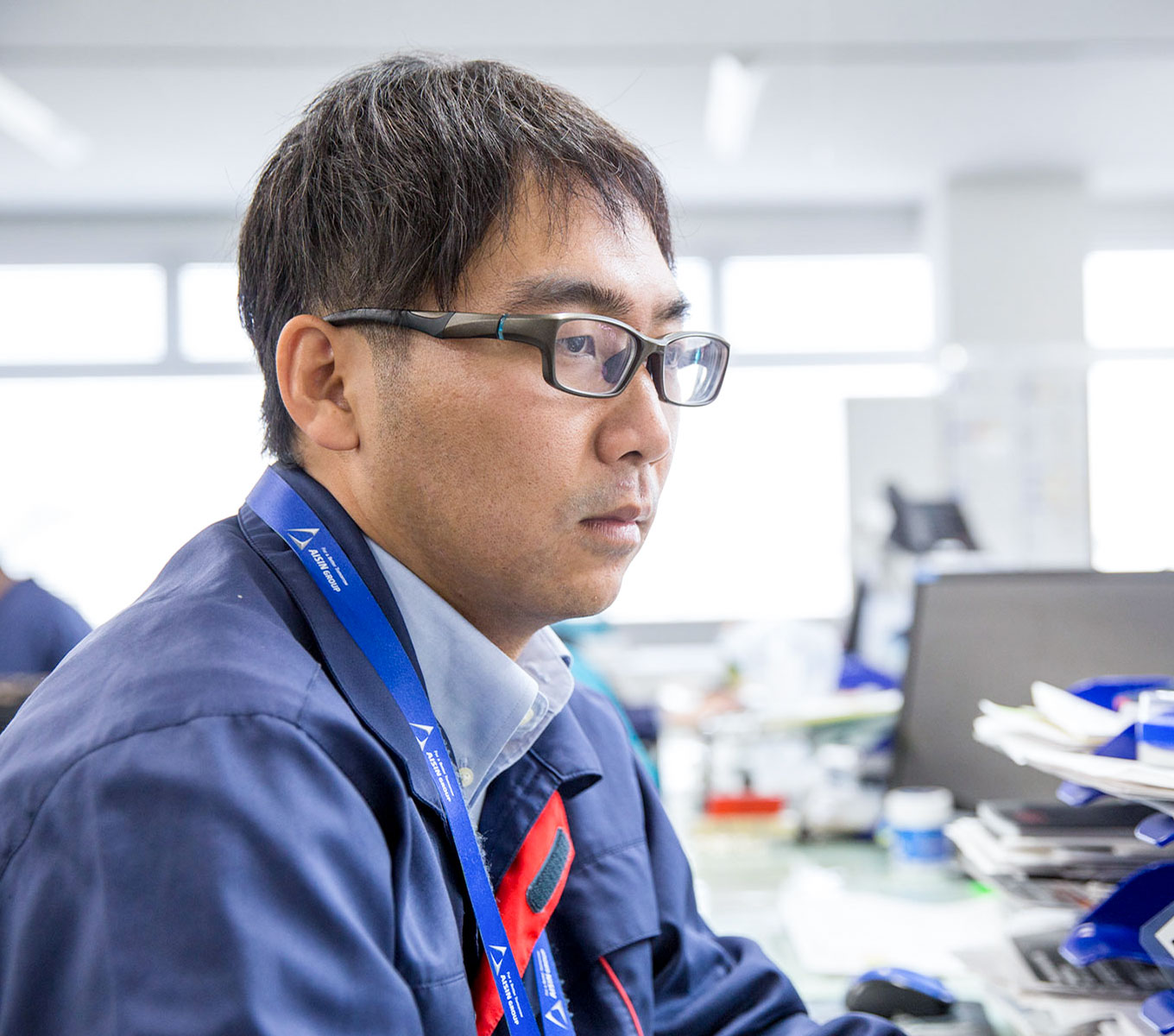
ギヤポンプ量産という
難題への挑戦。
ギヤポンプは、1対の歯車がケーシングの中で噛み合い、回転することでブレーキフルードを送り出す仕組みの油圧ポンプ。前のクルマと一定距離を保つために自動で車速を調整する「ACC」など、常時作動するような制御ブレーキでの活躍が見込まれる。従来製品よりも油の吐出脈動が少なく、優れた静粛性を備えるからだ。これは、快適な自動運転・高度運転支援の実現にギヤポンプが大きく寄与するということを意味する。
その反面、ギヤポンプは超精密製品であり、量産が非常に難しい。構成部品の加工精度が低いと油が漏れ、モーターの発熱の原因となるからだ。ブレーキ油圧は200気圧にもなるため、通常のギアポンプでは油漏れが発生してしまう。そのため、ブレーキ製品向けギヤポンプの加工精度は、1000分の1mmが求められる。その生産を移管し、量産しようというのが、アドヴィックスの計画。「ミクロンオーダーの精密機械を何万ものスケールで量産することが可能なのか――。」プロジェクトリーダーの鈴木は、生産技術を長年経験してきたが、これほど難しい案件ははじめてだった。
内製化が正式決定すると、社内横断でメンバーが招集され、プロジェクトの推進母体「ギヤポンプ生産準備部」が設置された。製品名が部署名になるのは異例中の異例。製品への期待の現れだ。工場への生産設備搬入開始はわずか数ヶ月後。それまでに生産ラインを設計し、工程ごとに必要な設備の仕様を決め、設備メーカーへの発注を終えなければならなかった。
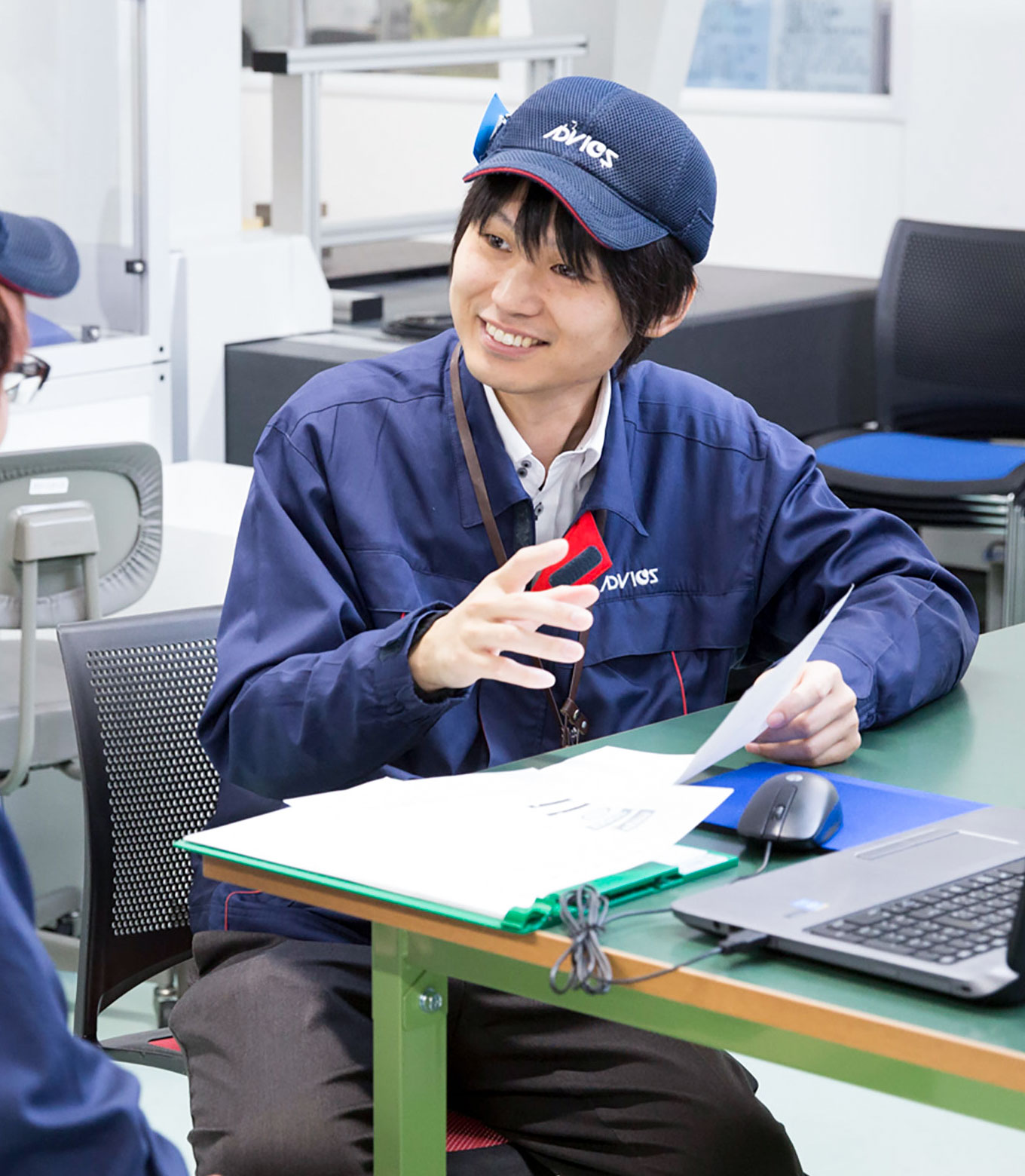
全員が同時並行で動いた
1年4ヶ月の総力戦。
プロジェクトの全体スケジュールを舵取りしたのは、事務系スタッフである生産管理部の福島だ。新製品を扱う新ライン。全員がゼロから製品を勉強しながらプランを組み立てる中、福島は指針となるマスタープランを作成。製造・生産管理・品質管理など関係部署すべての担当者30名近くを集め、ゴールとタスクを定めた。そして毎週のように会議を開き、それぞれの立場の意見を吸い上げていった。
まずは生産技術が動き出し、設備の配置・搬入を急ピッチで進めていった。並行して、製造と品質管理から20名余りが、ギヤポンプ量産ラインを有するデンソーに出向。実際に製造ラインに立ち、製造の手順や技術、品質管理のノウハウを実地で身につけた。
半年後、工場に続々と設備が運び込まれるようになると、そこへ出向を終えた20名が合流。設備と人が揃い、プロジェクトは佳境を迎える。試作を重ねながら品質のつくり込みと設備の最終調整(精度や能力確認)にあたる「工程整備」が行なわれる。もし立ち上げが遅れれば、カーメーカーへの製品の供給が滞り、納車を待っているユーザーに迷惑をかけてしまう。
重圧が背中に重くのしかかる中で、メンバーは結束をさらに強めた。スケジュールを確実に前へ進めるために部署を問わず全員で協力工場を訪ね、加工品質の確認や日程調整にあたったことも。多くのメンバーにとって、社外の協力工場にこれほど頻繁に出向くのははじめてだった。自分がやらねば——。誰の呼びかけがあったわけでもないのに、全員がそんな意識を共有していた。ラインが完成し、本番稼働のスイッチが押されたのは、それから数ヶ月後のことだった。
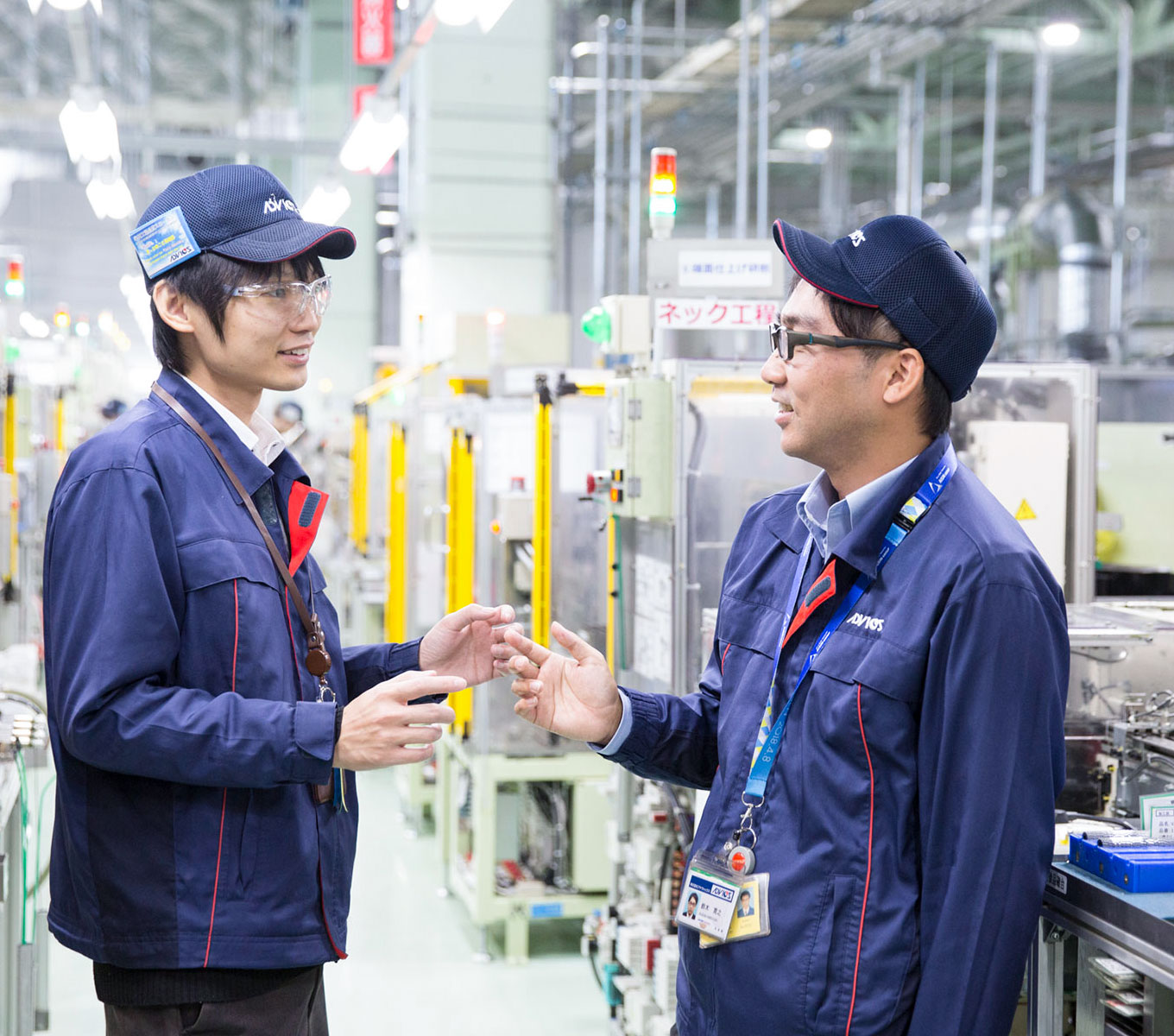
チームワークで乗り越えた
高く厚い壁。
わずか1年半足らずで、高く厚い壁を乗り越えた。参加メンバーが成功の要因として異口同音に挙げるのは、部門間や担当領域、さらに会社間も含め、あらゆる垣根を越えて存在したチームワークだった。鈴木や福島が主導していた毎週の合同ミーティングでは、困り事があれば互いに打ち明け合い、全員で共有し、解決策を考え、必要とあればどんなサポートもいとわず提供した。誰もが、重要なプロジェクトに参加している責任を自覚し、互いに補いあってひとつのゴールを目指す一体感が生まれていた。
「上司から裁量を与えられ、思い描いたことを思い通りに実行できる自由な空気が成功の要因でした」。と若手の宮下は語る。また、社内外を問わず異なるバックグラウンドを持つ多様な人材が結集したことで、既成のルールや価値観にしばられない柔軟な発想や行動が生まれたことに言及するメンバーも少なくない。
「他社と差別化し、競争に勝ち続けるには、高度化するニーズに対応できる技術を磨かねばなりません」。と鈴木。ギヤポンプ内製化の成功は、アドヴィックスがさらなる飛躍を遂げるための重要な一歩となった。